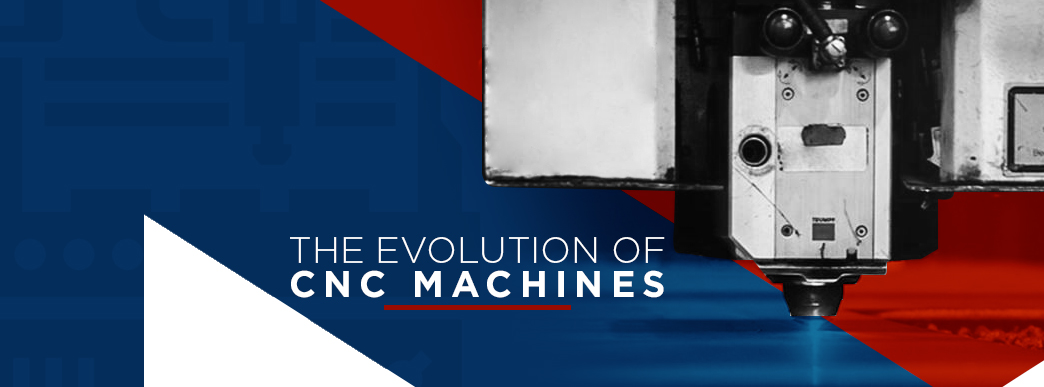
Polar coordinate command is a numerical control system in which all the works with are referred to a certain post. Placement is specified by the polar span as well as polar angle with respect to this post. Cutter payment is the distance you desire the CNC control to counter for the device span away from the set path.
Equipment precision can be enhanced remarkably by kept pitch error payment, which corrects for lead screw pitch mistake and various other mechanical positioning mistakes. Helical interpolation is a technique made use of to make large-diameter openings in workpieces. It enables high metal removal rates with a minimum of device wear. There are equipment regimens such as drilling, deep boring, reaming, touching, boring, etc that entail a collection of maker operations, however are specified by a solitary G-code with ideal specifications.

It additionally needs to withdraw at the exact same specific rate; or else it will shave the opening and also create an out-of-specified touched opening. Automobile scaling equates the specifications of the CNC program to fit the workpiece. Several various other sort of producing tools and production procedures are regulated by various other kinds of programmable CNC controllers.
There are two axis systems used in CNC, one for flat and also prismatic workparts and the various other for get rid of rotational symmetry. Both axis systems are based on the Cartesian coordinate system. cnc mill. The axis system for level and also prismatic parts contains 3 straight axes (x, y, z) in the Cartesian coordinate system, plus three rotational axes (a, b, c), as received Number 7.
The Only Guide for Cnc Lathe Machine
In the majority of maker device applications, the x- as well as y-axes are used to relocate and also position the worktable to which the part is attached, and the z-axis is made use of to regulate the vertical placement of the cutting device. Such a placing plan is ample for easy mathematical control applications such as boring as well as boxing of flat sheet steel.
The a-, b-, and also c-rotational axes specify angular settings about the x-, y- and also z-axes, specifically. To differentiate positive from unfavorable angles, the right-hand regulation is used. The rotational axes can be used for one or both of the following: (1) alignment of the workpart to present various surface areas for machining or (2) alignment of the tool or workhead at some angle about the component.
Equipment tools with rotational axis ability usually have either four or 5 axes; the three straight axes, plus 1 or 2 rotational axes. Many CNC systems do not call for all 6 axes. Number 7. 14. Coordinate systems utilized in mathematical control: (a) for level as well as prismatic job and (b) for rotational job.
The job rotates, this is not one of the regulated axes on many of these transforming machines. The course of a reducing device family member to the revolving work surface is defined in the xz airplane, where the x-axis is the radial place of the tool, as well as the z-axis is identical to the axis of turning of the component.
What Does Cnc Router Machine Do?
Hereafter beginning lies, the no position is connected to the machine device driver for the reducing device to be relocated under manual control to some target point on the worktable, where the tool can be quickly as well as properly positioned.( 2) Movement manage the heart of CNCThe most fundamental feature of any kind of CNC controller is automated, accurate, and also regular motion control.
These axes identify specifically and immediately the position of the work surface. Both most typical axis kinds are as discussed in the past, linear (driven along a straight path) and also rotating (driven along a course that the workpiece turns around) (cnc laser). Rather than triggering activity by manually transforming cranks and handwheels as is required on standard equipment devices, CNC equipments permit motion to be activated by servomotors under control of the CNC, and also assisted by the component program.
Figure 7. 15 shows the makeup of a straight axis of a CNC controller. In this situation, a command informs the drive electric motor to turn an exact variety of times. The rotation of the drive electric motor in turn revolves the round screw, which drives the straight axis. A responses tool at the contrary end of the round screw enables the control to verify that the regulated variety of rotations has taken location.
In comparison, a direct axis on a CNC machine tool is exceptionally specific. The number of changes of the axis drive electric motor precisely manages the quantity of straight activity along the axis. All discussions to this factor have thought that the outright mode of programs is made use of, where completion points for all motions are defined from the program zero point.