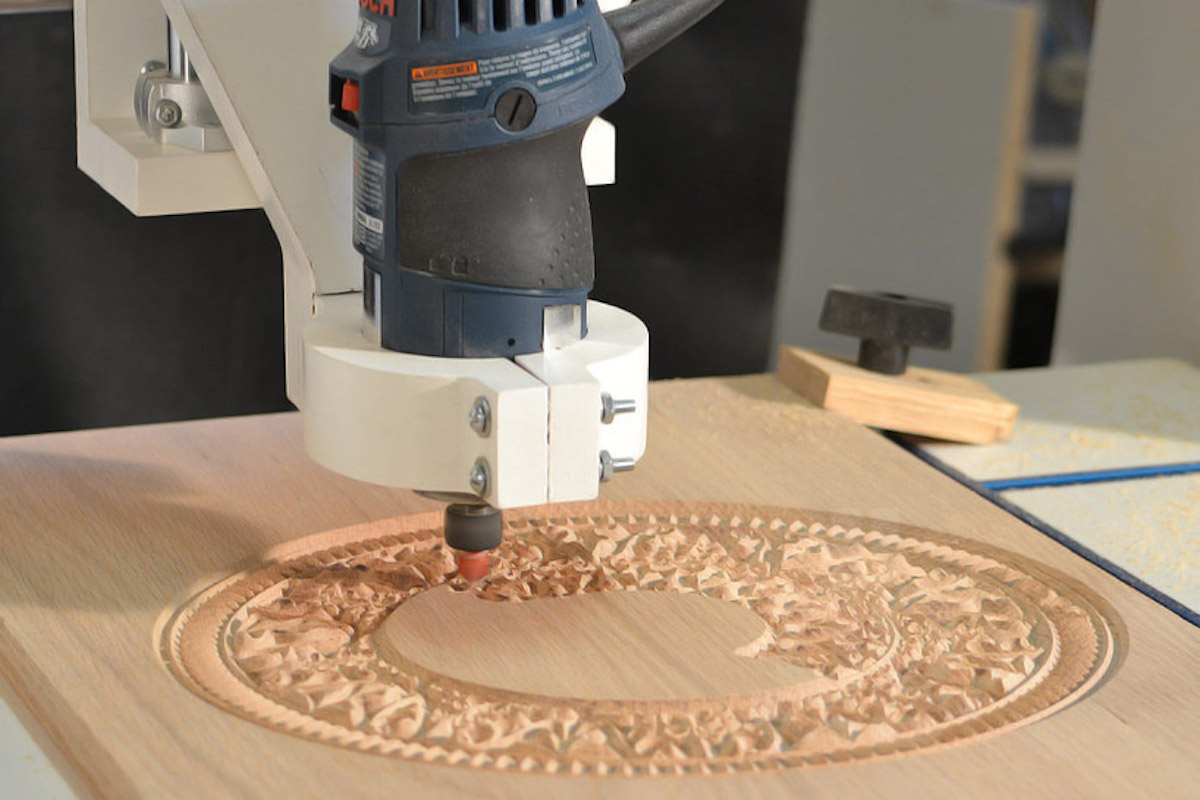
Polar coordinate command is a mathematical control system in which all the collaborates are referred to a specific post. Setting is defined by the polar span and polar angle relative to this post. Cutter compensation is the distance you want the CNC control to balance out for the tool span far from the configured course.
It permits for high metal removal rates with a minimum of device wear. There are device routines such as drilling, deep exploration, reaming, touching, boring, and so forth that include a collection of maker procedures, however are specified by a single G-code with proper parameters.
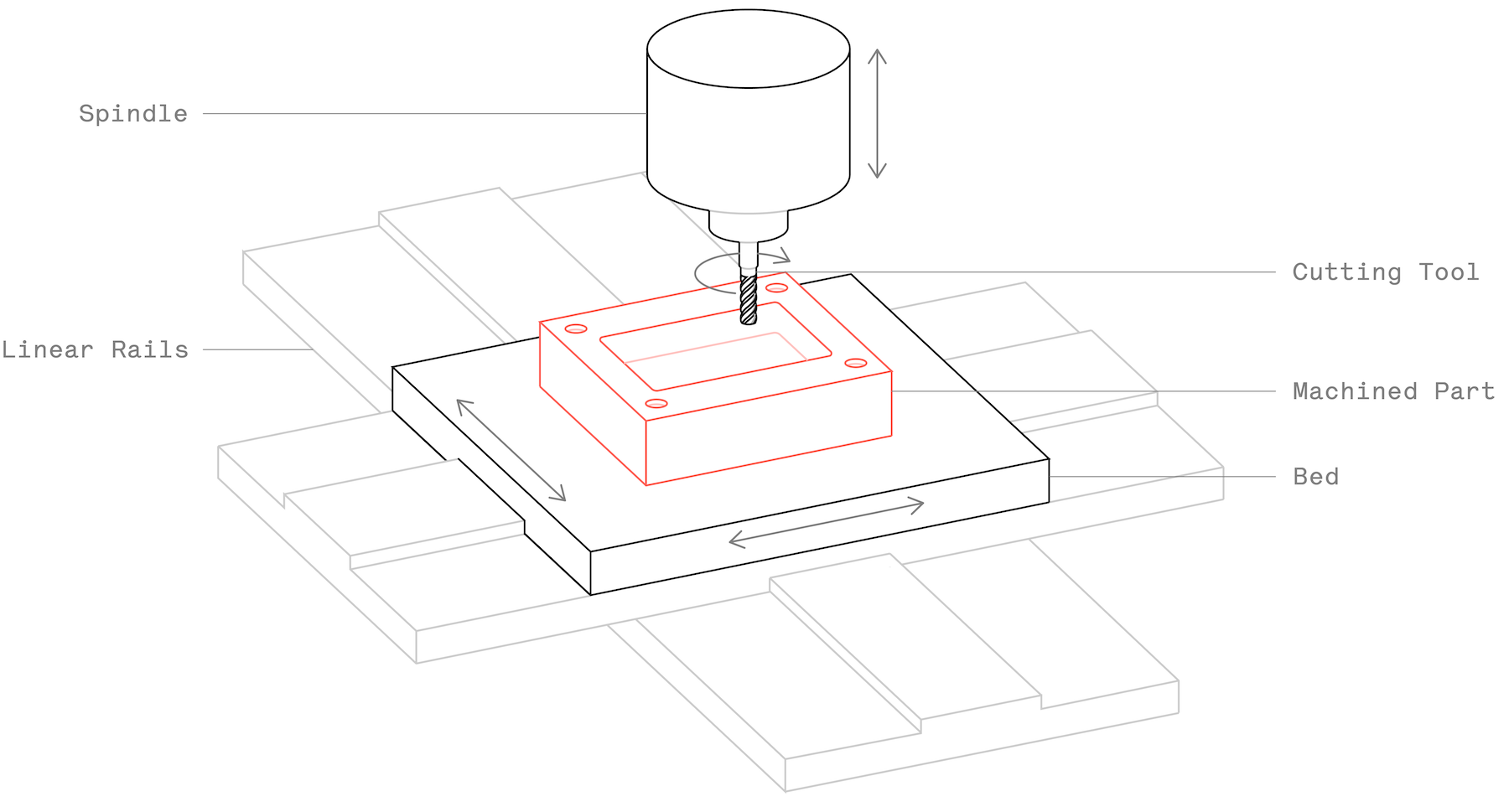
It additionally needs to withdraw at the same precise rate; or else it will cut the hole and create an out-of-specified tapped hole. Auto scaling equates the criteria of the CNC program to fit the workpiece. Lots of other sort of manufacturing equipment and manufacturing processes are regulated by various other kinds of programmable CNC controllers.
There are 2 axis systems used in CNC, one for level as well as prismatic workparts and the other for get rid of rotational balance. Both axis systems are based on the Cartesian coordinate system. cnc plasma cutter. The axis system for flat and also prismatic components includes 3 direct axes (x, y, z) in the Cartesian coordinate system, plus 3 rotational axes (a, b, c), as displayed in Figure 7.
Cnc Cutting Machine – Truths
In many equipment device applications, the x- and also y-axes are used to move and also place the worktable to which the part is attached, and also the z-axis is used to control the upright position of the cutting device. Such a placing system is ample for simple mathematical control applications such as exploration and punching of flat sheet steel.
The a-, b-, as well as c-rotational axes specify angular placements concerning the x-, y- as well as z-axes, specifically. To differentiate positive from negative angles, the right-hand policy is made use of. The rotational axes can be utilized for one or both of the following: (1) orientation of the workpart to provide various surfaces for machining or (2) orientation of the device or workhead at some angle family member to the part.
Machine devices with rotational axis ability typically have either 4 or five axes; the 3 direct axes, plus one or 2 rotational axes. A lot of CNC systems do not need all 6 axes.
The work turns, this is not one of the regulated axes on many of these turning equipments. The path of a cutting device relative to the turning work surface is specified in the xz aircraft, where the x-axis is the radial place of the tool, as well as the z-axis is identical to the axis of turning of the part.
The Only Guide for Cnc Router Machine
Hereafter origin lies, the no setting is communicated to the maker device operator for the reducing device to be moved under manual control to some target factor on the worktable, where the device can be quickly as well as precisely positioned.( 2) Activity regulate the heart of CNCThe many basic function of any kind of CNC controller is automated, accurate, and constant motion control.
These axes figure out precisely and also automatically the setting of the work surface. The 2 most typical axis types are as pointed out previously, linear (driven along a straight course) as well as rotating (driven along a path that the workpiece rotates around) (cnc milling machine). Rather than triggering movement by manually turning cranks as well as handwheels as is called for on traditional equipment devices, CNC devices allow activity to be actuated by servomotors under control of the CNC, as well as assisted by the part program.
15 reveals the make-up of a direct axis of a CNC controller. The rotation of the drive electric motor in turn revolves the sphere screw, which drives the straight axis.
In comparison, a straight axis on a CNC machine device is extremely specific. The number of changes of the axis drive electric motor precisely controls the amount of linear motion along the axis. All conversations to this factor have thought that the outright mode of programs is made use of, where the end factors for all activities are specified from the program absolutely no factor.